The construction sector is typically accused of being slow to embrace change and adapt to new technology and methods, particularly when it comes to administration and the back office. There’s no denying, however, that in some areas of the trade the industry is making great strides.
Modular construction is on the increase within both residential and non-residential projects for example, but what is it, and what can we learn from the benefits it brings?
What is modular construction?
Traditionally, the construction of buildings and other structures involves erecting them on-site from a concrete slab or footings. This process can take months or even years to complete. However, with the introduction of modern methods of construction (MMC), the process is becoming streamlined with projects being completed up to 50% faster.
Many government projects, not just in the UK and Ireland but worldwide, are now using this prefabrication method to speed up the build process. By way of example, in the wake of 2017’s Hurricane Maria in Puerto Rico, modular construction was utilised to quickly build more resilient homes and schools so that people in the area could return to a sense of normality as soon as possible.
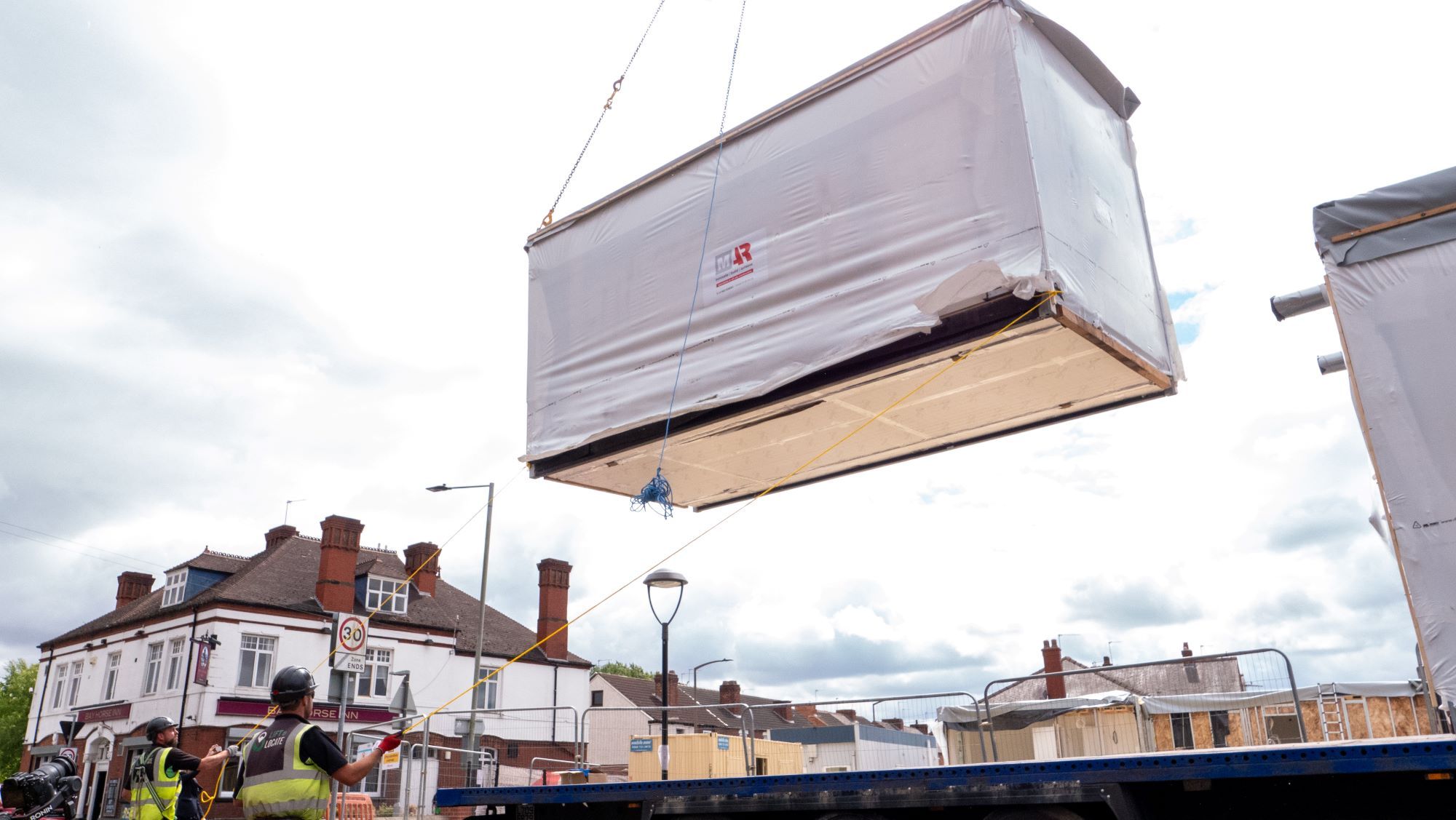
Benefits of modular construction
In its most basic form, modular construction refers to building a structure off-site and then transporting it to its final location. By working in a central, controlled factory environment, businesses can tap into several benefits associated with off-site construction, including reductions in material and labour costs, minimised on-site storage space, quicker completion and a faster ROI because buildings can be occupied sooner.
Mark Farmer, author of the Modernise or Die report, CEO of Cast Consultancy, and passionate MMC advocate said in a building.co.uk article, “Adopting modern methods of construction will allow the industry to hit vital targets on decarbonisation, building safety and better design.”
In 2020 Mark jointly authored a report with HTA Architects partner, Mike De’Ath laying out their ambitions to accelerate the role modular homebuilding plays as part of a more strategic approach to nurturing and mainstreaming the manufactured housing market. In the report, benefits outlined included support to advanced manufacturing, the creation of highly skilled jobs and productivity improvements in construction. Two of the key take-aways were:
- Modular manufacture is the biggest single game changer when it comes to additionality of new housing supply.
- Modular manufacturing can help deliver the UK Industrial Strategy’s skills, productivity, technology and carbon reduction objectives.
From legislation and administrative perspectives, pre-assembly makes it easier to comply with building codes and regulations as the factory-controlled environment affords more efficient quality control checks at every stage of the process.
CIF’s report – ‘Modern Methods of Construction’ in Ireland
In the current geopolitical environment, factors such as the cost of living crisis, unaffordable housing, and climate change are all impacting the adoption of modern methods of construction. As such, the Construction Industry Federation (CIF) put together a working group to report on the topic, publishing their findings in December 2021.
Throughout their report, CIF explored how modern construction methods are now crucial to the future of Irish construction, with modular and off-site manufacturing enabling higher quality standards of design, fabrication, testing, and certification.
The report also continued, describing how the increased adoption of modular and off-site construction in Irish construction should result in at least a 45% reduction in material use, alongside a 50% reduction in waste generation.
Given the materials used in off-site production tend to also have a much lower carbon footprint, with energy efficiencies made throughout the manufacturing process, organisations can rely on modern methods to continue on their journey towards government-set Net Zero goals.
Lessons for the back office
Advancements in construction, like modular building, can go a long way towards improving efficiencies and the long-term quality of work. For businesses looking for ways to get started, the FIS’ Digital Toolkit is a useful resource, for both on- and off-site work, as well as back office solutions.
Indeed, for a project to maximise the benefits of construction innovations, back office administration and business processes need to keep pace, employing modern methods too. Through the use of technology, construction businesses can begin to automate traditionally manual and time-consuming processes, ensuring efficiencies on all levels.
One company that has done just that is M-AR. A main contractor with a factory, M-AR Off-Site has the flexibility to work in the most appropriate and efficient way for any particular project – taking a modular approach or operating as a traditional contractor, or a hybrid of the two. But key to innovative working across the business is improved technology in their back office.
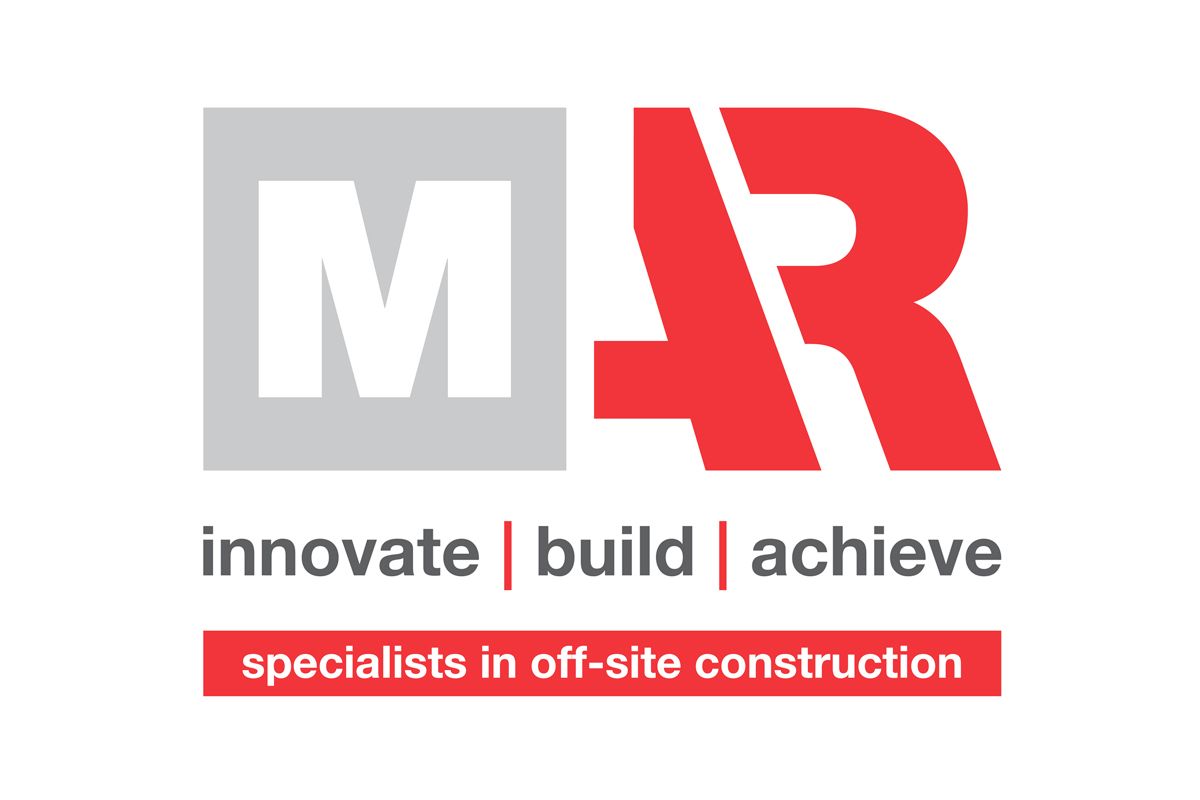
Their use of Payapps for example has changed what was a traditional process of managing applications for payment – using spreadsheets and manual methods – to one that is centralised, standardised and streamlined, allowing online collaboration with their subcontracting supply chain.
Ryan Geldard, Director at M-AR, said, “One of the benefits of a modular approach is that it’s a more predictable way to build – we can provide greater certainty around delivery so that our clients can more effectively plan their budgets, timelines and ROI.”
“In the same way, we can use technology in the back office to gain better predictability of supply chain payments and our cashflow, which is why we started using Payapps. In turn, Payapps allows us to provide visibility of application for payment status to our subcontractors so their cashflow is easier to foresee and manage too. Ultimately this ensures our projects stay on track, and we can continue to grow.”
Find out more
Get in in touch if you’d like to take a more modern approach in your back office, and achieve greater predictability of payments, final account and cash flow across your application for payment process.