Discover how major companies are deploying innovative techniques to enhance their construction procedures and boost the output of their supply chains.
The construction sector has a productivity problem. While productivity levels in other sectors such as manufacturing have nearly doubled over the past two decades, they have remained flat in construction. Now consider that more than 50,000 construction and real estate firms began this year in financial distress and you have a toxic mix. It means that boosting efficiency across all areas of construction procedures is business-critical – and this will only move the productivity needle if changes are applied throughout the supply chain.
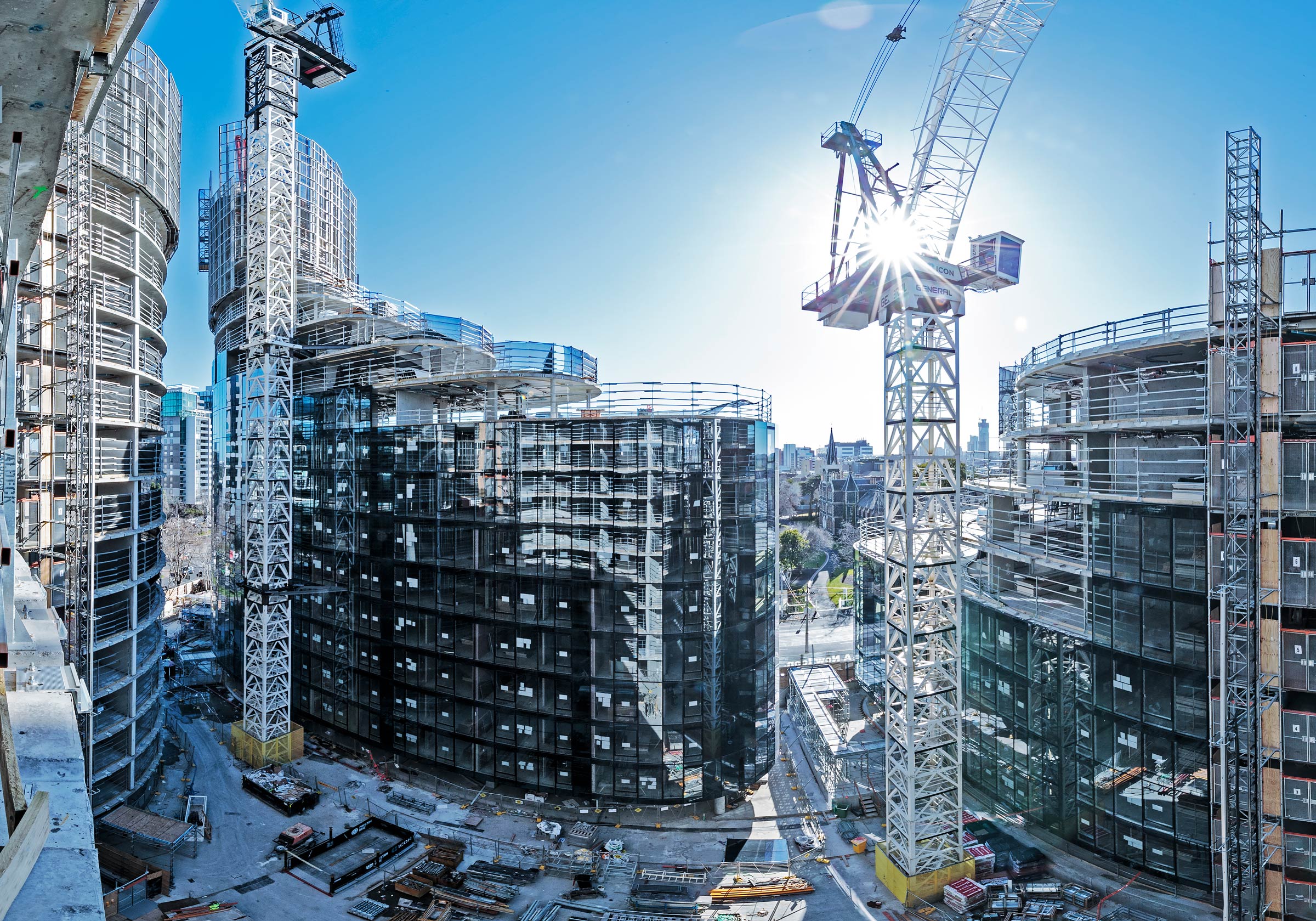
According to government figures, the construction industry is spending a total of £124 billion each year on supply chain management, but companies are not making the most from that sizeable chunk of investment. By examining what construction project planning strategies are being deployed by the big players to deal with supply chain productivity, insights can be gleaned that will benefit the entire supply chain – from massive multinationals to SMEs.
Building Information Modelling (BIM)
The UK construction sector is increasingly turning to 3D modelling to optimise its supply chain operations.
Speller Metcalfe
Project: Warwick Hospital
For its 12th project with South Warwickshire NHS Foundation Trust, Speller Metcalfe (SM) tried something different. It shared its BIM workflows with suppliers to make the supply chain more integrated and efficient. By analysing the 3D models in workshops arranged by SM, the subcontractor was able to identify areas that required attention before construction began. This covered everything from service routes and structure issues down to more detailed issues such as ceiling coordination, so the supplier was able to route mechanical and supply routes with ease in the limited space available, and identify any design issues as they arose.
This innovative approach also helped other contractors in the supply chain. The ductwork suppliers, for example, had access to the BIM model, and could now make sure their work fitted within the overall strategy. Thanks to BIM, Speller Metcalfe predicts that significant savings will be made on the project and that the number of man hours required on site have already been driven down.
Modular/off-site construction
Evidence shows that off-site modular construction can speed up project start and completion times by up to 50%, reduce labour costs and optimise construction project planning, offering companies all the benefits of factory-based quality while protecting profit margins.
Kier
Project: HMP Oakwood Prison
As part of its £185m new-build prison, lead contractor Kier brought in Balfour Beatty to supply water, heating/cooling systems, full-height service risers (incorporating drainage) plus plant rooms and an energy centre. Using a combination of BIM modelling and 2D drawings, Balfour Beatty was able to build these critical elements off site as prefabricated service modules.
Installation then took place – effortlessly and accurately. Adopting this prefab approach yielded vast productivity gains with a saving of 75,000 man hours on site and a host of other added benefits, including a reduction in waste, increased build efficiencies and more consistent quality.
Collaboration
For a sector obsessed with building unbreakable structures, it’s perhaps ironic that the way it operates is the polar opposite – fragmented and siloed. This is why supply chain collaboration is being embraced by the industry across more and more areas of construction procedure.
Amey
Project: Wessex Capacity Enhancement (Waterloo Station)
Collaboration was at the heart of a project to increase train and passenger capacity at Waterloo station and along the Wessex Route. Instead of working in corporate silos, Amey collaborated closely with Fairway, the transport infrastructure specialist, a strategy that saw the best people from each company brought in to form the bidding team – with any egos left outside the boardroom.
This collaborative approach was pushed out across multiple areas of construction project management with BIM models shared between all stakeholders in the supply chain. To keep in place key construction procedures when the team was disbanded, Amey and Fairway created a set of design parameters for future teams. This collaborative strategy has in effect ‘future proofed’ the integrity of the project’s supply chain for the years ahead.
Automation
The sector is notorious for relying on spreadsheets and paper-based processes to manage suppliers and their payments, wasting time and resources in the process – but forward-thinking companies are using software solutions to automate the payment process.
Built
Project: Payment Claims
Like many in the UK Construction industry, the Australian builder was chained to outdated, costly and manual systems when processing and managing payment claims from its subcontractors. They relied on paper-based, disparate processes that saw payment claims being posted, emailed and faxed in every conceivable format, creating a logistical nightmare. It forced managers to comb through each non-standard payment claim, struggling to check the details submitted were present and correct.
To deal with such a haphazard system, Built took the decision to implement a software solution specifically designed to handle the considerable challenges thrown up by the monthly payment claim process. Accessible on any device at any time, the platform selected allowed their subcontractors to prepare and submit their payment claims in a consistent, online set of forms. Built can now assess and process payment claims much more quickly, efficiently, and in a consistent format across all of its subcontractors and work packages. As a result, they have gone on record to say that the 3-4 days normally needed to process around 20 paymet claims has now been reduced to less than a day, saving time, effort and cost. It has in turn led to dramatic increases in payment efficiency so subcontractors can get on with what they’re supposed to be doing – building!
Solving the productivity deficit
Only by adopting such techniques and processes can the construction sector hope to boost productivity levels that have remained unchanged – and unchallenged – for over 20 years. By introducing the right technology and developing ever closer collaboration, the negative trend can finally be bucked as supply chain productivity is optimised. The end goal? To drive up ROI on supplier investment and ultimately, to protect those all-important profit margins now and in the future.
Takeaways
- Deploy BIM to enable all stakeholders in the construction process to understand and implement the build efficiently.
- Introduce off-site construction and modulation techniques to drive down costs and the number of man hours required onsite.
- Roll out software solutions to wipe out the construction sector’s over-reliance on dated payment processes that can act as a drain on time and resources.