The construction industry operates within the tightest of margins. As such, project delays and disputes can often occur due to many reasons.
But, can technology play its part in helping work take place correctly, and why is it necessary to get it right the first time?
Construction projects – the cost of getting it wrong
When a project goes right, all parties are happy. But, sometimes, it can go wrong – and when it does, it can be catastrophic, impacting relationships, supply chains and reputations. Whilst sometimes mistakes are entirely unavoidable, there is nothing more frustrating than work grinding to a halt because of an avoidable error.
Studies suggest that the measured direct cost of avoidable error across the construction industry is 5% of project value – above the average profit levels in the UK and costing approximately £5billion per annum. When unmeasured and indirect costs are considered, the situation becomes even worse. The figure rises to 10-25% – more than £20 billion annually in the UK alone. Such levels of loss can be difficult to accept, especially as businesses navigate supply chain issues, price hikes and ever-inflating costs. So, what can be done about it, and how can technology help?
The construction industry – getting it right
The construction industry has been on a mission to get things right first time. So much so that in 2017, a group of UK-based construction companies, experts and organisations got together to create the Get It Right Initiative (GIRI).
GIRI, a not-for-profit membership organisation, works to improve the sector by eliminating errors – reducing the annual £20bn+ bill. By raising awareness about the challenges of errors – and why they can extend beyond on-site – GIRI is on a mission to improve the industry.
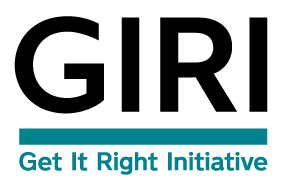
According to GIRI’s website, they’re working with members to meet five goals, which are:
• Creating a culture and working environment to get it right from the start
• Changing attitudes and harnessing leadership responsibility to reduce error and improve construction quality, productivity and safety
• Engage all stakeholders in eliminating error from inception, through operation, to completion.
• Share knowledge about error education processes and systems.
• Improve skills across the sector, creating a positive approach to pre-empting error.
Identifying potential errors within construction projects
Projects in construction are incredibly complex, with many moving pieces needing to come together in unison to ensure success. In several sectors, such as Fit-Out and MEP for example, these moving parts are often incredibly fast-paced, meaning increased likelihood of errors.
Speaking at a roundtable hosted by Construction News, Clifford Smith, Executive Director at GIRI, outlined that the first step to improving construction processes is to identify where the most significant potential for error appears. He commented:
“Interestingly, a lot of the root causes of error we found were mostly at the early part of the construction process – during the design and planning, and also the setting up of the project, and developing its culture around teamwork and collaboration.
“Errors are occurring on-site, but their root cause is much further up the project chain.”
Leveraging technology in the back office
Forward-thinking businesses perpetually strive for ways to improve their processes – and, as Cliff Smith alluded to, this goes beyond events happening at the coalface.
Take administration in the back-office for example – by leveraging technology here, not only can the quality of projects improve, but firms can improve both on- and off-site processes too. For instance, when thinking about construction supply chain payments, using technology to standardise payment applications from subcontractors means these documents are right first time, ensuring compliance and removing the need for time spent returning and adjusting submissions. Removing these potential delays to subcontractor payments provides improved cash flow predictability for all parties.
With timely reminders of payment notice deadlines, automated workflows, and a central online platform acting as a single source of truth, contractors get their timings right for payment notices and pay less notices. Equally, better communication and collaboration is achievable across all parties.
Digitising the typical paper and email trails and removing the need for payment applications to be submitted on error-prone spreadsheets provides all stakeholders with an accurate and clear view of the status of applications for payment. In short, technology can remove the threat of project delays and disputes due to missing or poor information.
Payapps: the key to getting it right
Payapps helps with getting things right in the back office first time round, which has positive implications for the rest of the project… and your supply chain.
For your organisation to benefit from technology – and get things right the first time – get in touch for a free software demo.